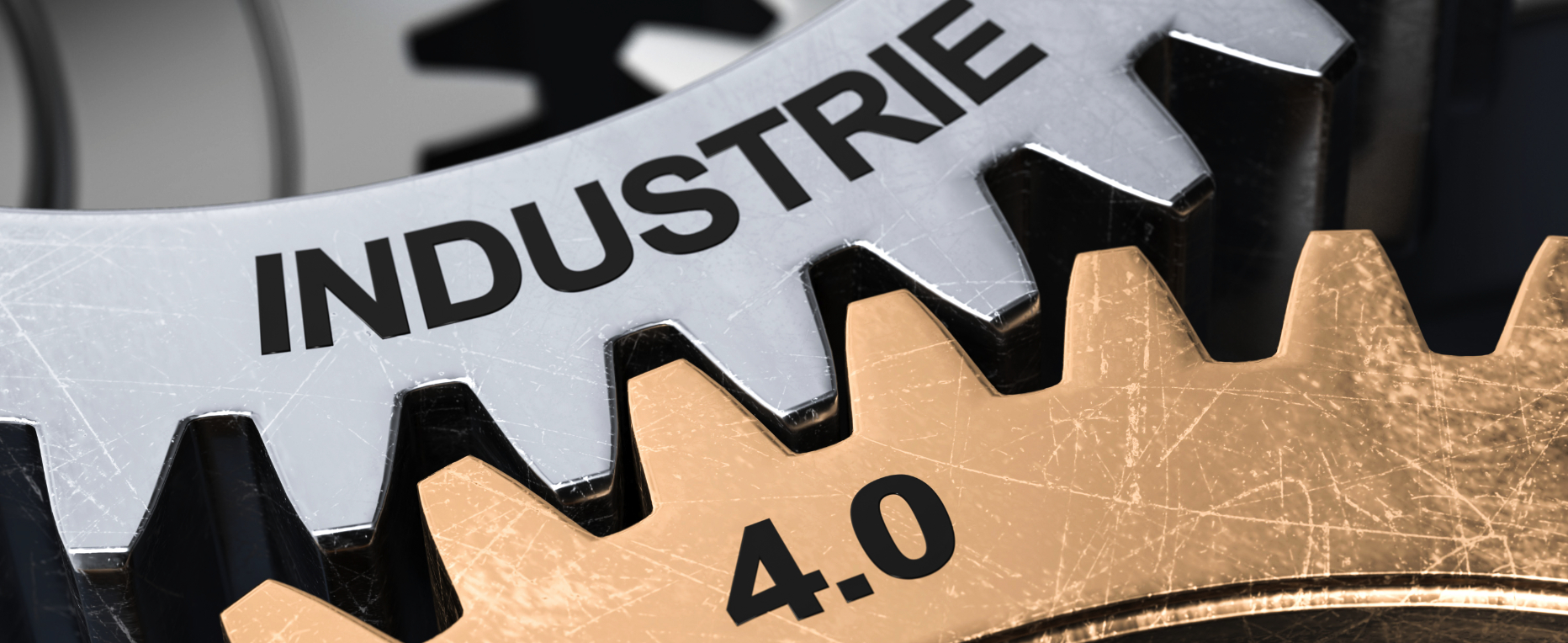
Higher productivity, optimal workload and extensive cost-savings – you can achieve all of this if you upgrade your machines to the latest technological standard. Retrofitting the electrics to the most modern hardware is beneficial and resource-efficient. Our retrofitting actions are not only aimed at operators of textile machines, but to anyone who wants to equip their existing facilities for the future.
Rapid implementation
You can’t afford for your machinery to have extended downtime – and it won’t come to that. Quite simply because we assume responsibility for overall planning, assembly, installation and programming. Our engineers are experienced in completing retrofitting rapidly and seamlessly. In this way, we can tackle projects of all dimensions.
Absolute Safety
Alongside our rapid pace, operational safety is our priority. We are CE-certified and adhere to the applicable EU safety regulations. The control cabinets and controllers that we deliver meet the current European EMF guideline. While the retrofitting work is being conducted, we establish a safe work environment for all co-workers.
100% Manpower
Our experienced team comprises specialists, who are masters of their trade – after all, they spent many years working for such machine manufacturers as Krantz, Stentex, Artos-Babcock and Moenus. Accordingly, they bring their full commitment to the job, irrespective of time and place.
For all machinery from KRANTZ | BABCOCK-ARTOS | MOENUS | STENTEX | BRÜCKNER | MONFORTS | ZIMMER, among others.
Why retrofitting?
Veraltete B&R-oder S5-Steuerungen lassen sich im Störungsfall nur unter großem Aufwand reparieren. Wenn Sie Subsysteme einbinden und automatisieren möchten, ist die moderne S7-Steuerung ideal. Weiterer Pluspunkt: Sie sorgen langfristig für einen störungsarmen Betrieb.
What is different?
Your equipment can be operated intuitively using a touch panel. You can manage recipe specifications for individual items and store process data in a central databank. The integrated measurement and regulation sensor technology measures delays, residual moisture and exhaust air moisture. Temperature regulation and width adjustment are also included in the upgrade. With the network connection, you benefit from rapid remote service, troubleshooting and problem-solving.
Why retrofitting?
Nowadays, the maintenance of PIV drives and Baumüller inverters is complex, as replacement parts are difficult to source. Modern gear motors are reliable, cost-reducing and more efficient. The motors are regulated using digital inverters from Lenze or Siemens.
What is different?
Alongside modern touch panels, you use recipe specifications and reproducible drive settings. Via a control centre with visualisation, you gain a complete overview of the drive. Using the detailed display, faults can be quickly corrected. The precise and stable speed and torque technology raises the product quality – all with a low level of maintenance effort.
Why retrofitting?
Fewer repairs, lower energy consumption, reduced costs: The precise, controller-operated temperature regulator makes it possible. And if a need for replacement parts were to arise, they are easy to obtain.
What is different?
The installation can be intuitively operated using a touchscreen. The exact temperature profile and the precise setting in the range of 0.5°C enhance the quality of your products. By storing your temperature profiles in the process databank, they can be reproduced at any time. Using a network connection, you have the choice of rapid remote service, troubleshooting and problem-solving.
Why retrofitting?
Would you like to adjust the spindles individually and thereby minimise the cost of maintenance and replacement parts? In that case, conversion to individual width adjustment using PLC control technology is recommended.
What is different?
You will have an overview of all of the spindles on the touchscreen. The exact angle monitoring ensures faultless processing. In addition, you can achieve optimal settings for the span image, thereby raising the quality of your products. The BCD encoders are replaced by absolute value encoders. Using the optional network connection, you can benefit from reliable remote service, troubleshooting and problem-solving.
Why retrofitting?
Liquid and natural gas burners require an upgrade from time to time to ensure that they adhere to exhaust emission standards. Furthermore, modern burner systems consume less power, are low-maintenance and improve product quality.
What is different?
You gain high-performance liquid and natural gas burners that incorporate safety equipment that corresponds to current standards. Modern burner systems can constantly maintain and regulate all temperatures from 80°C to 360°C. Replacement parts are readily available.
Do you have questions or would like further information?